How To Install Compression Packing
March 3rd at 6:23am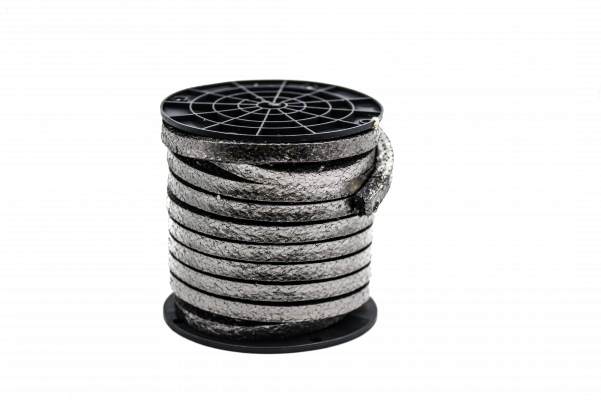
The importance of packing the pump correctly cannot be overemphasized. Many packing failures are due to incorrect installation of the packing. The following steps have been devised to ensure effective installation of packing on pumps:
- Remove all the old packing from the stuffing box: Clean box and shaft thoroughly and examine shaft or sleeve for wear or scoring. Replace shaft or sleeve if wear is excessive.
- Use the correct cross-section of packing or die-forming rigns: To determine the correct packing size, measure the diameter of the shaft (inside the stuffing box area if possible) and then measure the diameter of the stuffing box (to give the O.D. of the ring). Subtract the I.D. measurement from the O.D. measure-ment and divide by two. The result is the required size.
Cut...Don't Wind
![]() | ![]() |
Butt joint | Skive joint |
- When using coil or spiral packing, always cut the packing into separate rings: Never wind a coil of packing into a stuffing box. Rings can be cut with butt (square), bias or diagonal joints, depending on the con- struction. It is recommended that Centerlock® packing be cut only by butt (square) method. The following illustr- ations show these methods of preparing bulk packing. The best way to cut packing rings is to cut them on a mandrel with the same diameter as the shaft in the stuffing box area. If there is not shaft wear, rings can be cut on the shaft outside the stuffing box. Hold the packing tightly on the mandrel, but do not stretch excessively. Cut the ring and insert it into the stuffing box, making certain it fits the packing space properly. Each additional ring can be cut in the same manner, or the first ring can be used as a master from which the balance of the rings are cut. It is necessary that the rings be cut to the correct size. Otherwise, service life is reduced. This is where die-cut rings are of great advantage, as they give you the exact ring size for the I.D. of the shaft and the O.D. of the stuffing box. There is no waste due to incorrectly cut rings.
Install one ring at a time: Make sure it is clean, and has not picked up any dirt in handling. If desired, lubricate the shaft inside of the stuffing box. Seat rings firmly (except PTFE filament and Graphite yarn packing, which should be snugged up very gently, then tightened gradually after the pump is on stream). Joints of successive rin
gs should be staggered and kept at least 90o apart. Each individual ring should be firmly seated with a tamping tool. When enough rings have been individually seated so that the nose of the gland will reach them, individual tamping should be supplemented by the gland.- After the last ring is installed, take up bolts finger tight or slightly snugged up. Do not jam the packing into place by excessive gland loading. Start pump, and take up bolts until leakage is decreased to a tolerable minimum. Make sure gland bolts are taken up evenly. STOPPING LEAKAGE ENTIRELY AT THIS POINT WILL CAUSE THE PACKING TO BURN UP.
- Allow packing to leak freely when starting up a newly packed pump: Excessive leakage during the first hour of operation will result in a better packing job over a l
onger period of time. Take up gradually on the gland as the packing seats, until leakage is reduced to a tolerable level. Never try to stop leakage entirely, unless we indicate it is safe to do so - Provide means of lubricating the shaft & packing through the lantern ring by supplying water, oil, greease or liquid handled in the pump. Fittings for
this purpose are standard on many pumps (consult pump manufacturer's manual).Typical stuffing box with lantern ring - cross section
- If the stuffing box has a lantern ring, make sure that the lantern ring is slightly behind the fluid inlet so that it will move under the inlet as follower pressure is applied.
- Replace packing when leakage cannot be controlled by further takeup on the follower gland.
- On centrifugal pumps, rotary pumps, and reciprocating pulps, about 80% of wear is on the outer two packing rings nearest the gland. However, each additional ring does throttle some fluid pressure. On most machines, there must be enough rings so if one fails, another does the sealing, and the machine need not be shut down.
Wear /pressure load curve
The mechanical pressure curve above shows eight packing rings. The first five rings do the majority of the sealing. The bottom three do little sealing, but are needed to fill the available space. The advantage of using fewer rings is less rod wear. Also, the stuffing box design is simpler and takes less material. But, wear isn't the only problem. With high temperatures, high pressures, corrosive chemicals, or abrasive particles in the fluid, more rings may be the only solution for some services. In such cases, the bottom ring contacting the fluid may have the most wear from these severe service conditions.
Other Posts

ElastaGraph - A Revolutionary Metal Gasket Technology
Read Article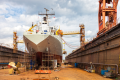
How do IMPA Marine Numbers Map to Phelps Industrial's Products
Read ArticleHow to chose O-Ring material for your fluid sealing applications
Read Article
Troubleshooting O-Ring Failures
Read Article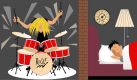
Material for Sound Proofing and Sound Dampening
Read Article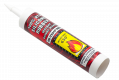